A step by step guide to the zinc electroplating process. Cleaning and pickling as described above for alkaline cyanide zinc processes activates and prepares steel parts for plating.
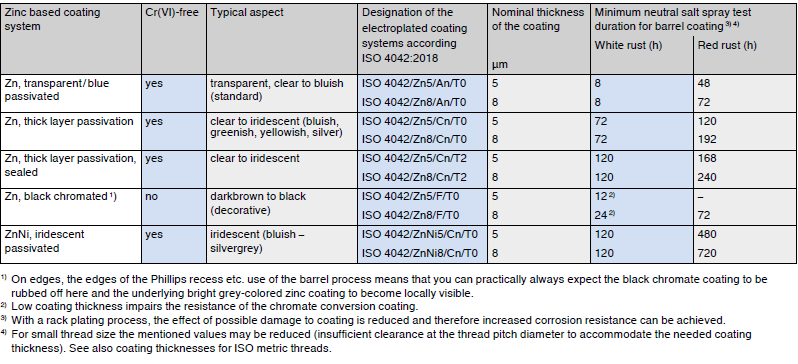
Galvanic Process Technical Information Bossard Group
Zinc plating process steps. After plating hexavalent and trivalent chromate conversion coatings can provide up to 500 hours to white salt formation per astm b 117. Preparing the plating solution zinc plating requires the immersion of the substrate into a specially formulated. Typical steps in electroplating process. On the commercial scale zinc electroplating is done by the following steps. Preparing and cleaning the surface its essential to thoroughly clean the surface of the substrate prior to plating. Cleaning and pickling as described above for alkaline cyanide zinc processes activates and prepares steel parts for plating.
Zinc electroplating steps step 1. Steps of commercial zinc electroplating. With reverse current electroplating in which at regular intervals plating current is reversed for a second or so the polarization effect becomes negligible even with the very high overall speed of plating. Activation or pickling of the metal involves removal of oxides and scales from the surface by using various acid. Cleaning of the substrate is done in order to remove any dirt rust oil etc from the surface. Surface of the metal is cleaned in alkaline detergent type solutions and it is treated with.
Step 2 activation of the substrate. To finish the preparation of the substrate it goes. The process shown below takes about 90 minutes to complete. The first step is to clean the substrate the metal you wish to plate. Step 1 cleaning the substrate. Zinc plating methods one method for applying a zinc layer to a metal part is via hot dip galvanization.
Therefore while performing the electroplating process steps appropriate current densities should be used. The flux is generally a solution of zinc ammonium chloride. After plating chromate conver sion coatings that can provide up to 1000 hrs to white salt formation per astm b 117 are available and may provide a cost effective alternative to alloy plating. The part is then dipped into a vat of molten zinc that has a layer of flux floating on top of the zinc. Proper cleaning and. Any contamination on the surface of the.
Heres an overview of how a typical zinc plating process works. Acid in order to remove any rust or surface scales. The surface must be free of contaminants for bonding to take place. This is the process for plating steel aerospace parts with cadmium.